Eine weitere Technologie, die schon seit mehrere Jahren für das Carbon-Capture erforscht wird, ist das Oxyfuel-Verfahren. Anders als andere Abscheidungsmethoden zielt dieses nicht darauf ab, CO2 aus dem Abgasstrom einer Industrieanlage oder eines Kraftwerks zu entfernen. Stattdessen soll das Abgas von vornherein so verändert werden, dass möglichst wenig andere Gase wie Stickoxide und Schwefeldioxid anfallen und fast reines CO2 entsteht.
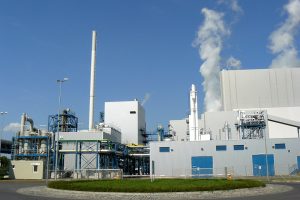
Reiner Sauerstoff als Verbrennungshelfer
Für das Oxyfuel-Verfahren als nachgeschalteten Prozess wird das Rauchgas des Kraftwerks oder der Fabrik in einen Brennofen geleitet und dort unter Zuführung reinen Sauerstoffs noch einmal verbrannt. Das Resultat ist ein Abgas, das aus gut 90 Prozent CO2 und aus Wasserdampf sowie einen geringen Restgasanteil besteht. Der Wasserdampf kann auskondensiert werden, so dass am Ende fast reines CO2 übrig bleibt, das weiterverarbeitet oder gespeichert werden kann – soweit die Theorie.
In der Praxis allerdings ist auch die Abscheidung von CO2 durch Oxyfuel mit hohem Aufwand und Kosten verbunden. Vor allem die Gewinnung und Bereitstellung von reinem Sauerstoff für die Rauchgasverbrennung treibt die Kosten in die Höhe, hinzu kommen zusätzliche Reinigungsschritte, um Restgase zu entfernen. Eine von 2008 bis 2014 im Kohlekraftwerk Schwarze Pumpe in Brandenburg betriebenen Oxyfuel-Pilotanlage zeigte, dass dieses Verfahren bei Kohlekraftwerken zu Wirkungsgrad-Einbußen von acht bis 14 Prozent führt. Oxyfuel war damit nicht weniger kostenintensiv und aufwendig als gängige CO2-Abscheidung durch Aminwäsche und Co..
Option für die Zementindustrie?
Als deutlich lohnender könnte sich die CO2-Abscheidung mittels Oxyfuel-Technologie allerdings in der Zementindustrie erweisen – sie ist immerhin für acht Prozent der globalen CO2-Emissionen verantwortlich. Bei der Zementherstellung wird die Oxyfuel-Verbrennung nicht erst beim Rauchgas am Ende der Prozesskette eingesetzt, sondern schon beim Brennen des Zementklinkers. Für dieses wird das gemahlene Calciumoxid zusammen mit Silikaten und Eisenoxiden in Drehöfen bis auf 1.450 Grad erhitzt.