Schon heute sind Rapid-Technologien in einigen Bereichen nicht mehr wegzudenken. So zum Beispiel in der Dentaltechnik. Individuelle Produkte wie Zahnersatz oder Gebisse lassen sich mit generativen Verfahren schneller und preisgünstiger fertigen als mit herkömmlichen Methoden. Eine Laser-Sinter-Anlage stellt beispielsweise täglich mehr als 500 Zahnkronen her, mit traditioneller Gusstechnik schafft ein Zahntechniker gerade mal zehn.
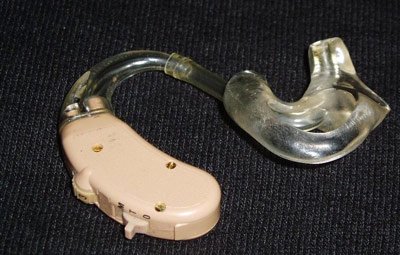
Rapid-Technologien ermöglichen auch die Fertigung passgenauer Hörgeräte auf Knopfdruck. Dazu wird einfach mit einem 3D-Scanner der äußere Gehörgang vermessen und diese Werte als Datenmodell in einen Rechner eingegeben. Am Computer lässt sich das virtuelle Gehäuse nach mechanischen und akustischen Tests optimieren. Danach wird es mittels Lasersintern oder Stereolithographie gefertigt. Heute werden weltweit bereits mehr als 40 Prozent aller Hörgeräteschalen generativ hergestellt.
Greifer nach Fischflossen-Art
Aber auch Konsumgüter lassen sich bereits in kleinen Stückzahlen herstellen. So gibt es schon erste lasergesinterte Möbel, Lampen und Accessoires auf dem Markt. Zu den Unternehmen, die generative Fertigungstechnologie erfolgreich einsetzen, gehört die Festo AG in Esslingen bei Stuttgart. Die Firma hat zum Beispiel einen bionischen Greifer nach dem Vorbild der Fischflosse entwickelt. Drückt man mit dem Finger leicht gegen die Schwanzflosse einer Forelle, so knickt diese nicht in Druckrichtung weg, sondern bewegt sich zum Finger hin. Möglich macht das der Flossenstrahleffekt.
Der „FinGripper“ besteht aus drei Fingern in Form der Fin-Ray-Struktur – ähnlich der Schwanzflosse. Trotz seiner komplexen filigranen Struktur lässt er sich kostengünstig mit Selective Laser Sintering herstellen. Der besondere Vorteil: Das Bauteil ist um 90 Prozent leichter als ein herkömmlicher Greifer aus Metall.