Bisher ist Epoxidharz nicht recycelbar, weil die vernetzte Polymerstruktur irreversibel aushärtet. Doch jetzt hat ein Forschungsteam eine neue Variante dieses Kunststoffs entwickelt, die seine hohe Stabilität behält, ihn aber dennoch wieder einschmelzbar macht. Möglich wird dies durch Einfügen phosphorhaltiger Verbindungsmoleküle, die feste, aber reversible Bindungen zwischen den Polymerketten ausbilden. Das neuartige Epoxidharz eröffnet damit auch die Chance, faserverstärkte Verbundstoffe zu recyceln.
Epoxidharze sind widerstandsfähige und vielseitige Kunststoffe. In Kombination mit Glas- oder Kohlenstofffasern werden sie beispielsweise zur Herstellung von Bauteilen für Flugzeuge, Autos, Züge, Schiffe und Windkraftanlagen verwendet. Solche faserverstärkten Kunststoffe auf Epoxidbasis haben auszeichnete mechanische und thermische Eigenschaften und sind viel leichter als Metall.
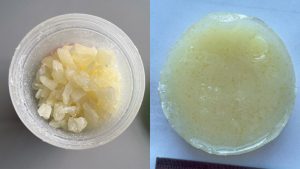
Warum Epoxidharz nicht recycelbar ist
Der Nachteil jedoch: „Heute sind faserverstärkte Kunststoffe praktisch nicht recycelbar, außer unter extremen Bedingungen, die die Fasern beschädigen“, erklärt Erstautorin Wenyu Wu Klingler von der Eidgenössischen Materialprüfungs- und Forschungsanstalt Empa. „Haben sie einmal ausgedient, werden sie verbrannt oder in Deponien entsorgt.“ Dadurch gehen auch die in die Kunststoffmatrix eingebetteten Kohlenstofffasern verloren.
Der Grund für die mangelnde Recycelbarkeit der Epoxidharze liegt in ihrer chemischen Struktur. Bei dieser Art von Duromer-Kunststoffen sind die Polymerketten besonders engmaschig miteinander vernetzt, was diese Materialien stabil macht. Gleichzeitig verhindert diese irrreversible Vernetzung aber auch ihr Wiedereinschmelzen. Ist das Epoxidharz ausgehärtet, bleiben die Querverstrebungen im Polymernetzwerk dauerhaft fest und das Material lässt sich nicht mehr verformen.